top of page

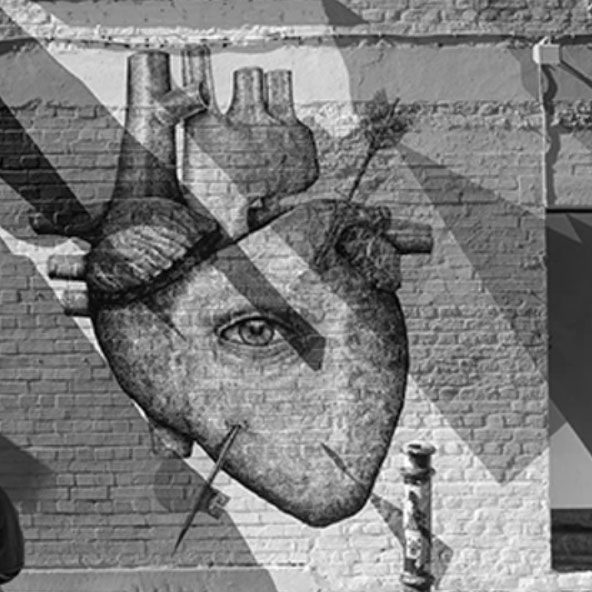
title. project 12
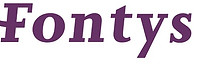
Mijn groepje bestond uit David, bink, Tijn en ik
Beta werelden: mens en medisch
Opdrachtgever:
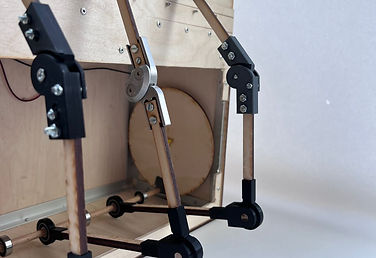
Fontys Paramedische Hogeschool is een instelling voor paramedische opleidingen in Nederland, met een focus op praktijkgericht leren en samenwerking tussen studenten en professionals in de gezondheidszorg. Gijs van Lent onze opdrachtgever, is een docent aan de Fontys University for Allied Health Professionals, hij is gepassioneerd over zijn vakgebied en geeft les in Paramedisch.
De opdracht
Onze opdracht bestaat uit onderzoeken of ge3D-printen scharnieren de dure aluminiumscharnieren voor knieortheses kunnen vervangen. Om productie ervan te vereenvoudigen en kosten te verlagen. Belangrijk onderdeel van het onderzoek is het testen en optimaliseren van het geprinte scharnier, om er voor te zorgen dat het sterk genoeg in en aan allen eisen voldoet.
Hypothese
Onze Hypothece is "Wij denken dat het kunststof scharnier een metalen scharnier bij een knieorthese kan vervangen."
Het onderzoek
Om het onderzoek te kunnen beginnen moesten we eerst een scharnier 3d-printen.
Dat is ook het deel van het project waar ik voor al mee bezig heb gehouden.
De ontwikkeling van een scharnier voor een knieorthese was voor al gericht op
kostenbesparing en verbeterde functionaliteit. Het ontwerp is geïnspireerd uit een
bestaande scharnier wat hier onder te zien is.Dit scharnier onderging diverse
aanpassingen om aan specifieke eisen te voldoen, zoals soepele werking,
krachten kunnen doorstaan en langdurige bruikbaarheid. we zijn tijdens het maken van
het scharnier door heel veel verschillen de versies gegaan die allemaal weer iets
beter waren dan de vorige ontwerp. De grootste aan passingen die we hebben gedaan
is het gebruik van kogellagers en het verminderen van onderdelen wat er voor zorgt
dat de speling wordt verminderd en daardoor de algehele sterkte van het scharnier
vergroot. De uiteindelijke versie, samengesteld uit geprinte onderdelen, wordt
gesmeerd met kaarsenwas voor een soepele
werking. Dit resulteerde in een functioneel ge3D-print scharnier voor knieortheses.
Nu we een scharnier hadden die werkt was het zaak om deze te gaan testen. Om dit te doen deden we drie soorten van testen. Als eeste test gaan we het scharnier zelf om doen en kijken of het scharnier beschadegingen krijgt en of allen bewegingen gemaakt kunnen worden of dat je daar in belemmerd word. Als tweede test gingen we de kracht van het scharnier testen, door er gewichten aan te hangen. Dit hebben we in twee richtingen gedaan namelijk tegen het scharnier in dus de verkeerde kant op. En ook in de richten 90 graden op de bedoelde richting. Het is helangrijk dat dit sterk genoeg in want het scharnier moet er voor zorgen dat je je knie niet kan overstrekken of verdraaien. De derde test bestond uit het scharnier heel vaak heen en weer bewegen. Om dit te testen hebben we een maschine gemaakt die een loop kan simuleren. Het uithoudings vermogen van het scharnier testen is belangrijkk om dat de verzekering wil dat het scharnier minimaal 2 jaar mee moet gaan anders zullen zijn het niet verzekeren. De maschine ziet er als volgt uit. Je ziet dat er drie scharnieren op de maschine zitten aangesloten
deze scharnieren worden heen en weer bewogen. Dit moet een keer of
3.6 miljoen keer gebeuren om het aantal stappen te simuleren die worden
gezet in 2 jaar.
De resultaten
Het scharnier kwam heel goed uit de test. Want tijdens de eerste test
hebben we gemerkt dat als je het scahrnier om hebt veel ondersteunig
ondervind. Ook konden we aan het scharnier geen schaden zien na de
testen die we hebben gedaan wat ook heel positief is.
Tijdens de tweede test kon het scharnier omgerekent in de tegegestelde
richting een gewicht van 88 kg houden en 90 dragen op het scharnier kon
hij 61 kg houden. Dit is meer dan genoeg want je hebt er twee per been en
dan ook nog de knie voor stabilisatie wat meer dan genoeg is. De laatste test hebben we helaas niet kunnen uitvoeren omdat de maschiene tegen wat technieche problemen aan liepen. Waar door we de resoltaten van deze test ook niet hebben. Maar we denken dat het scharnier de 3.6 miljoen keer wel kan halen. Want door de kogellagers is er weinig plactic tegen plactic dat gaat slijten.
De conclusie
In conclusie, na het uitvoeren van verschillende tests en onderzoek, kunnen we bevestigen dat onze hypothese "Is het mogelijk om het huidige aluminium scharnier te vervangen met een ge-3D-printe versie?" inderdaad klopt. Onze bevindingen tonen aan dat ge-3D-printe kunststof scharnieren geschikt zijn als vervanging voor metalen scharnieren. De positieve resultaten van onze tests bevestigen de duurzaamheid en functionaliteit van deze scharnieren, terwijl de voordelen van kunststof, zoals kostenefficiëntie en aanpasbaarheid, hun aantrekkelijkheid vergroten voor orthopedische toepassingen. In het kort, ons onderzoek ondersteunt de haalbaarheid van het gebruik van ge-3D-printe kunststof scharnieren als alternatief voor metalen scharnieren.




bottom of page